前言
随着我国可持续发展战略的实施,国家对单位GDP的能耗控制指标不断细化。作为重要过程设备的换热器在石油、化工、冶金、核电、建材等行业的热量回收和综合利用中发挥着越来越大的作用。
“十一五”以来,我国在大型炼油、大型煤化工、大乙烯等项目的建设中投资力度加大,规模也越来越大。和大型化的成套装置相适应,诞生了许多大型的换热设备。为了全面提高换热设备的传热能力,我国在换热设备的选型和研究上做了许多卓有成效的工作,主要包括三个方面的内容:研究和采用包括高通量换热管在内的各种强化传热元件技术;对大型管壳式换热器进行攻关;在高效传热结构的基础上研究大型缠绕管式换热器和大型板壳式换热器。除此以外,我国在大型板式换热器的国产化中也取得了一定的进展。
目前大型板式换热器主要应用于核电和海洋工程,这些领域采用国产化板式换热器的数量有限;同时由于受到使用环境的影响,某些强化传热的方法受到限制或者应用效果并不显著。我国换热设备的研究主要着眼于高效结构和整体可靠的协同性上。因此具有乐观应用前景的主要是大型管壳式换热器、大型缠绕管式换热器和大型板壳式换热器[1-2]。本文将对这三种换热设备近年来的国产化技术进展进行分析,并指出存在的问题和发展方向。
1、大型管壳式换热器的技术进展
环氧乙烷/乙二醇(EO/EG)是生产聚酯的主要原料,是乙烯工业衍生物中的重要产品。国外的生产规模已从早期的7万t/年发展到目前的68万t/年。“十一五”期间,我国的环氧乙烷总产量达到450万t/年。其中最具规模的是中国石化在天津和镇海乙烯项目建设中的大型的EO/EG装置(天津45万t/年、镇海65万t/年)。在EO/EG装置中,无论是SD工艺还是DOW化学公司工艺,工艺流程中都广泛应用了大型换热设备。镇海和天津采用的工艺为美国DOW化学公司技术,在国内为首次应用。在镇海EO/EG装置,换热面积10000m2以上的换热器有三台,6000m2以上的有两台;在天津EO/EG装置,换热面积8000m2以上的换热器有三台。两套装置中4台10000m2以上的换热器如表1所示。

这些换热器在设计制造中的难点主要如下。
(1)公称直径远大于GB151和TEMA的推荐值,在现行的国内外标准中,对此类换热器没有完全适用的计算方法;尤其是大直径、长换热管的管板计算,即使在金属壁温温差较小的情况下,其管壳程之间的膨胀量差也造成可能设置膨胀节。如果不设置膨胀节,管板的厚度需要大幅度地加厚。国家标准中压力容器膨胀节只能用于设备直径小于2000mm,超出的只能由供货商进行特殊设计和制造。
(2)国内的换热管一般长度不超过12m;对于接近和超过20m长且具有特殊要求的奥氏体不锈钢换热管,质量得不到保证。
(3)缺少对大型管壳式换热器设计中管束振动和防振技术的认识。大型管壳式换热器壳程介质流量较大,当流体横向穿越管束时,管子受到卡门漩涡和紊流抖振的影响,可能激发管束振动和声振动。如果管束振动剧烈到一定程度,将导致换热管的疲劳破坏或者换热管撞击折流板孔边而被切断。为此,不仅要从设计上使换热管的固有频率避开卡门漩涡频率,同时要从结构上实现有效支撑,降低管束间的横流速度。
(4)复杂的内部结构是保证工艺要求的前提。国外工艺商经常将反应、吸收等工艺和过程换热组合在一起,换热设备经常带有复杂的喷淋、扩散结构部件以及异型的插入结构。由于不能深入理解工艺商的目的,也制约了此类换热设备的国产化。
(5)大型管板的制造技术。由于大型管板的金属材料的耗量大,不仅增加了锻制的难度,甚至还需要拼焊。如何拼焊管板并保证材料性能的一致性,大型管板表面堆焊的防变形技术、大型复合板管板的加工工艺等都是重点研究的问题。
(6)大型管壳式换热器的组装技术。大型管壳式换热器换热管数量巨大,甚至超过一万根。这不仅给管板和折流板的钻孔精度提出了很高的要求,同时管子长、折流板多、管束重也使穿管的难度成倍增加。尤其是小直径换热管刚性差,很难控制挠度。因此,既要研究最佳的装备工艺,又要研制设计出合适的工装,保证穿管的顺利实施,不影响换热设备的操作性能。
(7)小直径换热管与管板的连接与检测技术。我国换热设备采用胀焊并用时大多为强度焊加贴胀,而国外许多设计中采用的连接方式是强度胀加密封焊。当换热器上(前)管板在高速流体冲刷状态下运行时,管板和管子的焊接接头难以保证密封的寿命要求,采用强度胀加密封焊的结构更为可靠。
但是对小直径换热管的胀接技术以及接头质量的检测技术,我国和国外的差距还很明显。
基于上述情况,这4台10000m2以上的换热器只有E-6111循环气冷却器实现了国产,其他三台换热器分别由韩国的Doosan和印度的Larsen&Toubro生产。
为了尽快实现EO/EG换热器和EO反应器这类大型换热设备的国产化,中国一重、中国石化南化公司化机厂等单位充分利用各自企业在我国石化设备制造中的优势,开展了多项研制攻关工作。其中,中国一重利用其在加氢反应器和核反应堆容器中的设计制造经验,探索大型换热器的材料、结构、制造工艺等关键技术[3-4],在大型换热器的国产化中取得了突出的业绩。表2列出了中国一重完成的典型大型管壳式换热器。
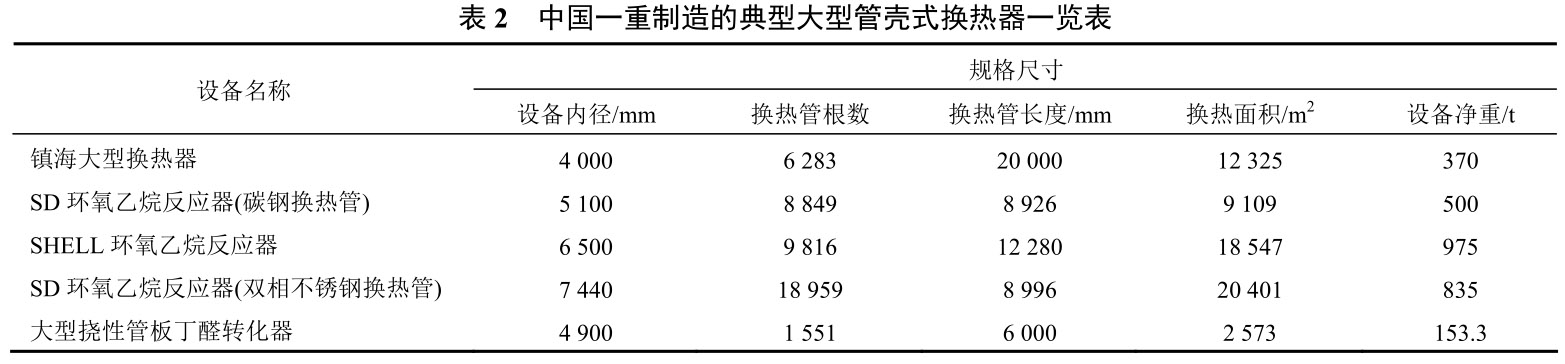
“十一五”期间,我国在大型管壳式换热器设计制造中取得的主要技术进展。
(1)设计技术上有了长足的进步,这种进步首先表现在大型换热器的设计中,传热流动设计和强度设计的协同性有了显著的提高。充分理解和预测可能发生的载荷组合,较好地处理了温度场、流场和力场的耦合,同时运用了全模型有限元分析对超过标准的主要受压元件进行设计和评定。
(2)研究并制定了大型管壳式换热器中许多专门材料的订货技术要求。先后完成了《SA302C钢板材购技术条件》、《SA508Gr3Cl1锻件技术条件》、《SA210GrA-1换热管订货技术条件》、《SA213-304/304L换热管订货技术条件》、《SA789S31803换热管订货技术条件》、《丁辛醇装置换热管订货技术条件》等专门技术文件。从几何参数到综合性能为大型管壳式换热器的国产化提供了保证。
(3)实现了长度30m以内重要材料换热管的国产化。以常熟华新特殊钢有限公司和江苏银环精密钢管股份有限公司为代表的企业已经能够自主研制满足国外工程公司技术要求的高精度换热管。其中SA213-304/304L双等级不锈钢换热管已在EO/EG换热器上得到应用(图1),SA789S31803双相钢换热管已在EO反应器上得到应用,φ88.9mm×3.2mm碳钢换热管已在丁辛醇装置转化器上得到应用。
(4)在管板制造工艺上取得了一定的突破。凭借着中国一重和上海重型的锻造能力,我国在锻制管板上的加工能力已经步入世界的先进行列。在大型丁辛醇转化器(图2)的制造中,中国一重锻造完成了合肥通用机械研究院的专利设计结构——带有柔性连接环的大型薄管板[5-6]。在镇海EO/EG换热器的研制中,中国一重先后完成了大型管板堆焊输入的数值研究,采用反变形技术保证了管板的平面度要求。
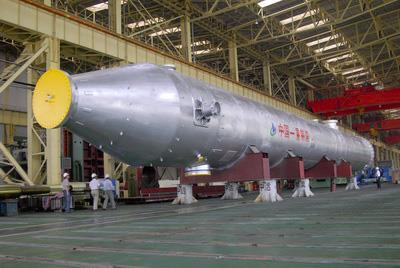
图1镇海EO/EG装置循环气冷却器
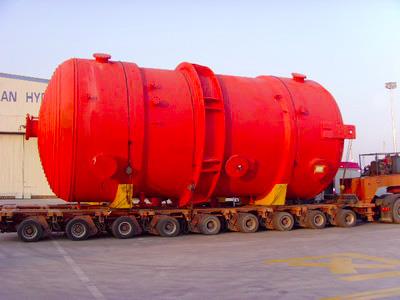
图2某丁辛醇装置丁醛转化器
(5)壳程设计技术日臻完善。大型管壳式换热器壳程管束支撑结构的设计,既要考虑到壳程的流场和温度场,又要兼顾到对管束振动的预防。在镇海EO/EG换热器的研制中,采用了折流板窗口区不布管、采用标准要求的最小折流板(支持板)管孔间隙、折流板之间增设支持板、增加流通通道、减小换热管支撑跨距、壳程入口处增加防冲杆等措施防止管束振动的发生。在大型转化器和反应器的设计中,采用了壳程纵向流动的技术,通过设置隔栅结构或者多孔支持板结构,既强化了壳程的换热,又增加了管束的刚性,保证了管束整个轴向和径向的温度控制。
(6)胀焊并用技术有了新进展。对于密封性能要求较高以及承受振动等场合,换热管与管板的连接接头普遍采用了胀焊并用的工艺。在大型管壳式换热器的制造中,既采用了强度胀和密封焊技术,也采用了强度焊加贴胀的技术。在镇海EO/EG换热器的制造中采用了上下管板不同设计的连接接头,上管板采用了平齐式密封焊加强度胀设计,下管板采用了外伸式密封焊加强度胀设计。工艺程序都采用了定位胀+自动焊+强度胀。在反应器中制造采用了强度焊加贴胀的工艺技术,针对低合金钢高强度钢的材料特点运用了电磁感应技术对焊接接头进行了消应力处理。
(7)采用了先进合理的组装技术。以管板为模板进行折流板系的加工和格栅的组焊,在折流板系的组装中采用了激光定位对中技术,保证了管孔的同心。在格栅的组装中,将格栅叠在一起进行试穿,控制了格栅的总体平面度和水平挠度。大型反应器现场分段组焊时,严格控制了因筒节对接可能造成的管孔对中偏差的累积放大。从四个角度检测了筒体的直线度,并将筒体的纵环焊缝全部打磨至与母材平齐。在筒节上开孔和组焊接管时,采取了有效的防止筒体变形和不圆度超差的措施。
(8)运用了多种先进的检测技术。在大型管壳式换热器的研制中,采用了TOFD技术对多段筒体的对接环缝进行了无损检测。采用了射线检测方法对换热管与管板的焊接接头进行了抽检。采用了氦质谱检漏技术对换热器管头的致密性进行了检测等。组合检测技术的应用,大大降低了设备缺陷的隐藏概率。
重要石化领域大型管壳式换热器的研制成功,标志着我国管壳式换热器的设计与制造水平上了一个台阶,对我国未来标准规范的制修订提供了有益的范例,同时也推动了我国高端换热管行业的技术进步。大型管壳式换热器也使我国的科研人员对换热器管束流体诱导振动的发生和预防有了进一步的认识。
2、大型缠绕管式换热器
和传统的管壳式换热器相比,缠绕管式换热器具有显著的特点:结构紧凑,单位容积具有较大的传热面积;换热系数较高;抗振动、耐高温差引起的热膨胀性能好;介质温度端差小,不可逆损失小;密封可靠性高、介质压力高;介质流畅、不存在换热死区;多种介质同时参与换热、不同介质之间无压差要求;换热器易实现大型化。缠绕管式换热器的典型结构形式如图3所示。
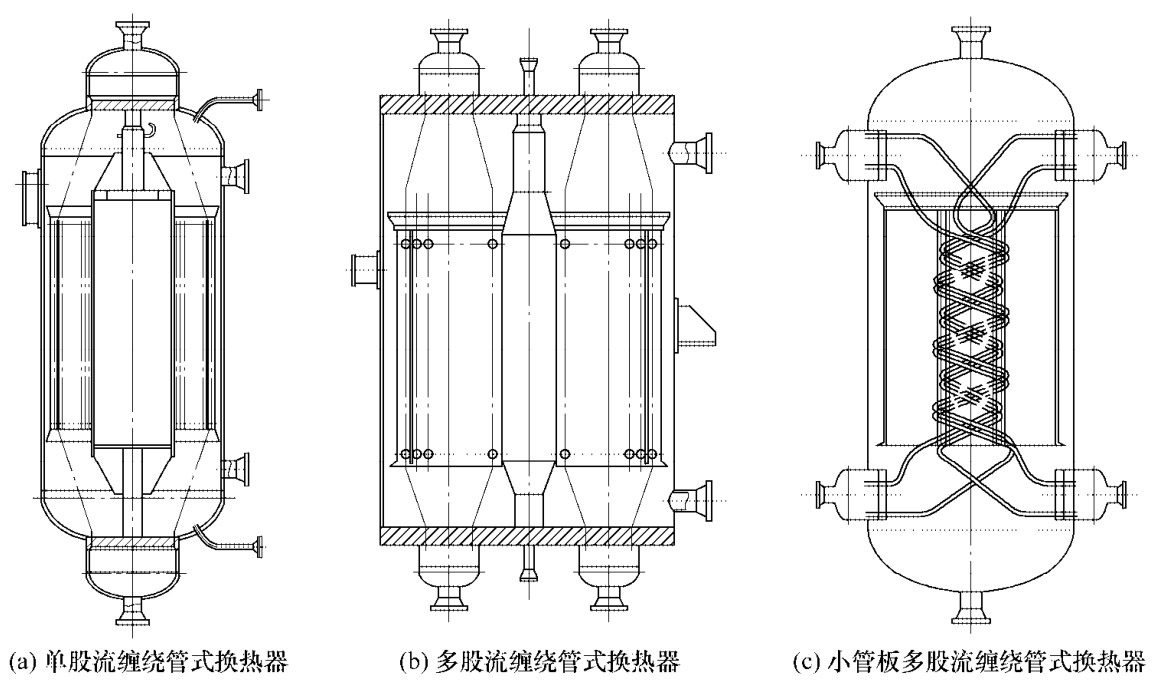
图 3 缠绕管式换热器的典型结构形式
缠绕管式换热器在中国的应用源于进口的空分装置和化肥成套装置的低温甲醇洗系统。直到上个世纪末,缠绕管式换热器的应用和更换仍依赖于进口。主要的技术难点如下所述。
(1)缠绕管式换热器尤其是多股流缠绕管式换热器的传热与流动的工艺计算方法;目前国际上通用的HTRI和HTFS软件都没有相应的计算模块。
(2)各种复杂的管板结构,包括单股流管板、多股流管板和小管板结构,其中大部分管板的布管区域不同于GB151,而且管板两端的管箱结构形式和GB151也都不同。
(3)超长奥氏体不锈钢焊接钢管的制造质量,影响到缠绕管式换热器的可靠性。
(4)大型缠绕管式换热器的组装技术。
(5)缠绕质量和管束的检测技术。
合肥通用机械研究院、镇海石化建安工程有限公司在国家十五重大技术装备研制攻关计划、“十一五”国家科技支撑计划的支持下,对缠绕管式换热器的传热与流动、材料、设计、标准、制造、应用等环节的诸多技术问题进行研究并取得突破。典型大型缠绕管式换热器如表3所示。
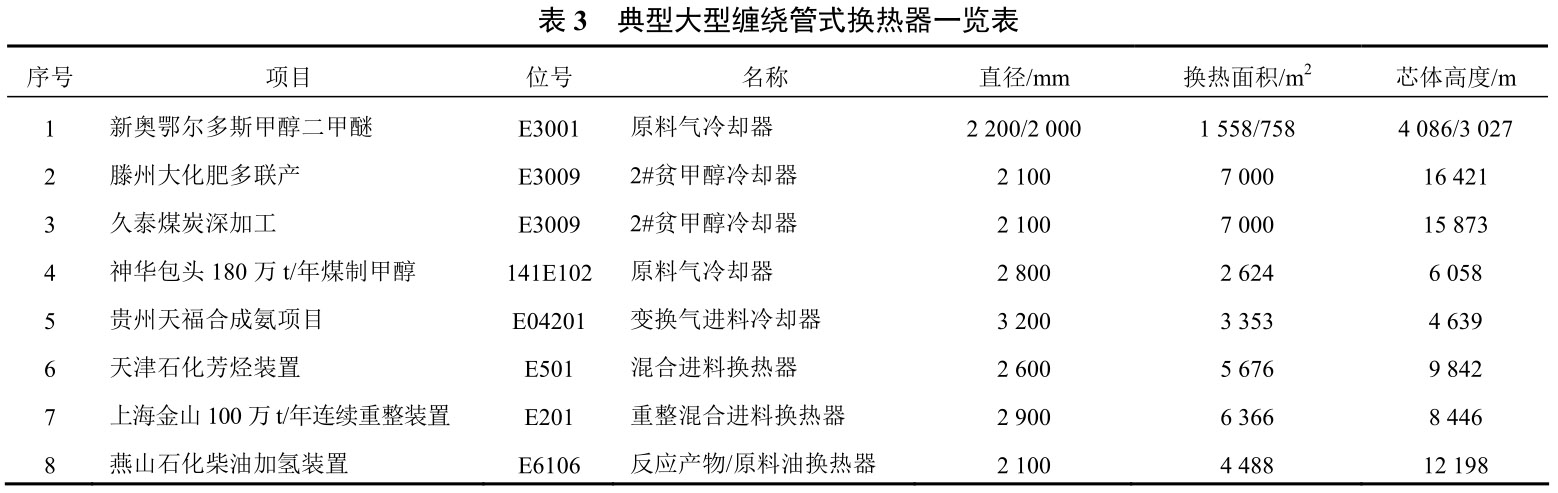
在“十一五”期间,大型缠绕管式换热器的主要进展。
(1)实现了多股流缠绕管式换热器的全面国产化,解决了低温甲醇洗领域多股流缠绕管式换热器各个阶段的技术问题,具有自主知识产权的工艺计算软件的准确性在多次应用中得到验证。我国在甲醇领域的缠绕管式换热器的规模已进入世界先进水平,图4为久泰煤炭深加工项目和滕州大化肥多联产项目制造的中国最大的贫甲醇冷却器,换热面积为7000m2。
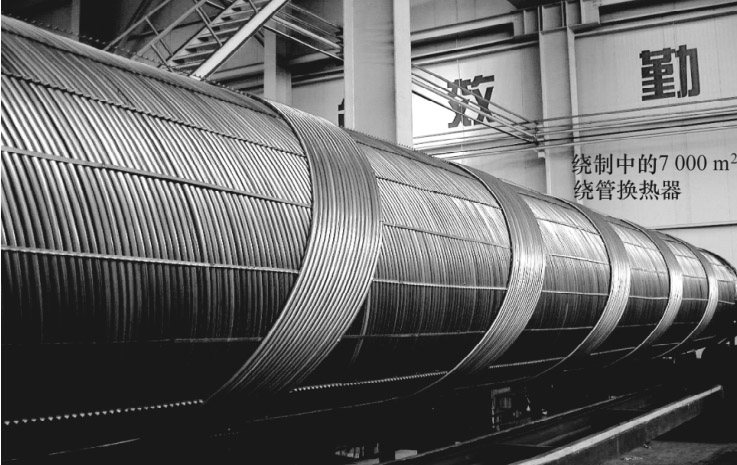
图47000m2贫甲醇冷却器
(2)完成了世界上第一台加氢裂化装置高压缠绕管式换热器的研制(图5),并在中国石化镇海炼化分公司150万t/年加氢裂化装置中成功使用[7]。研制过程中,获得了高温时效状态下换热管缠绕变形率的推荐值,完成了镍基合金堆焊的低焊接残余应力2.25Cr-1Mo钢对接接头的设计,完成了镍基合金封筒焊缝的超声检测技术研究,并应用射线检测技
术对换热管与管板的焊接接头进行了检测,保证了换热管与管板焊接接头的零泄漏。高压缠绕管式换热器为我国高温高压领域缠绕管式换热器的应用积累了宝贵的经验。
(3)基于高压缠绕管式换热器的加氢裂化流程本身也实现了一次变革,不仅使传统加氢裂化流程图5世界上首台加氢裂化装置高压缠绕管式换热器更加简捷,而且减少了高压换热器的数量,减少了加热炉的数量。新加氢裂化装置采用两台换热器高压缠绕管式换热器的流程,改变了原来7台高压螺纹锁紧环换热器的流程,热端温差小,使得加热炉的负荷显著降低,节能效果明显。对于150万t/年加氢裂化装置,一年可以减少燃料消耗在1100万元以上。另外,采用高压缠绕管式换热器的重量只有170t左右,采用螺纹锁紧环式换热器的金属重量却达280t,金属材料的消耗量显著下降。流程的简捷带来设备的减少,使装置的泄漏点减少,装置的可靠性得到进一步提高。
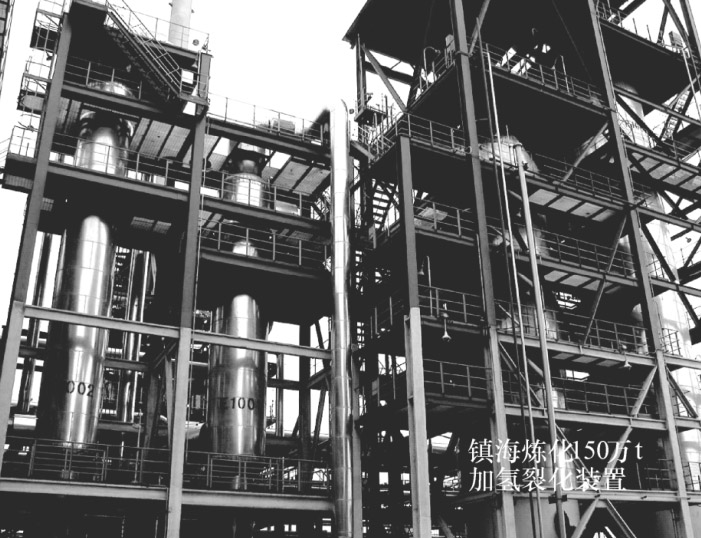
图 5 世界上首台加氢裂化装置高压缠绕管式换热器
(4)对低温甲醇洗原料气冷却流程实现了创新。装置的大型化后,单一的多股流缠绕管式换热器虽然可以简化流程,但设备巨大,带来的综合经济效益差。对于原料气和尾气处理量大的低温甲醇洗装置,原料气冷却器可以采用组合型流程替代原来的单一多股流缠绕管式换热器流程。在其中的单股流缠绕管式换热器中,可以将原料气和尾气的流路进行对调,注意流量的分配,既可以保证性能,又可以节约大量的金属消耗。优化后总传热系数由106.06W/(m2 •K)提高到130.30W/(m2 •K),增加了22.64%,传热性能得到提高,原料气换热器Ⅱ的换热面积由3224m2 减小至2624m2 ,并满足生产工艺的要求。管程、壳程的高、低压介质对调后,缠绕管式换热器的壳体壁厚变薄,设备质量减小50%,
在保证壳程安全的情况下,金属材料节省显著,设备投资大大减少。这种工艺创新已经在新奥鄂尔多斯双甲工程和神华煤基烯烃180万t/年甲醇项目中得到成功应用[8]。
(5)奥氏体焊接不锈钢换热管的应用得到快速的发展。我国放弃了德国低温低合金钢换热管的技术路线,在低温和高温领域应用在缠绕管式换热器的核心传热元件立足于奥氏体焊接不锈钢换热管,少量采用精密不锈钢无缝钢管。奥氏体焊接不锈钢的单根换热管长度已超过100m;在四种奥氏体不锈钢牌号上,不锈钢焊接钢管已可以在小于10.0MPa的非极度危害的介质上应用,超过了GB151标准规定的6.4MPa的限制。
3、大型板壳式换热器
板壳式换热器是将板式换热元件的高效性和壳体承压能力特点相结合的换热设备,主要应用于炼油重整、芳烃歧化和异构化等装置。随着装置能力的不断提升,板壳式换热器的大型化不仅是打破国外技术封锁的需要,也是进一步实现装置节能降耗的需要。
大型板壳式换热器研制攻关的主要难点如下所述。
(1)超大型板壳式换热器波纹板片开发及制造技术。如何保证与超大型板壳式换热器相适应的超宽板型的传热与流体力学性能,开发出高精度的模具和成型装备,保证板片具有冲压减薄量小,残余应力小、承压能力高、强度高、成品率高等特点,是研制的最大难点。
(2)建立专用焊接生产线,保证板片焊缝的密封性能及焊缝强度,同时又能满足大批量工业化板片焊接需要。
(3)大型板束的整体结构设计,包括板束在轴向方向的热膨胀结构和板宽方向的柔性连接结构、均匀高效的进料分布器结构、基于有限元分析和压力试验相结合的板束强度和刚度的研究、板束各部件连接的合理性研究。
(4)高腐蚀性场合特种材料板片的成形、焊接技术和腐蚀性能研究。
(5)基于可靠性的超大型板壳式换热器的制造、检测技术及应用指南。
甘肃蓝科石化高新装备股份有限公司在“十五”、“十一五”国家相关科研计划的支持下,开发出国产首台10000m2 大型板壳式换热器,在大型板壳式换热器的研究和应用上取得了显著的进展。(1)开发出了流体分布与传热性能兼顾的先进板片(图6);创造了整板分次步进模压成形工艺,配套大开档油压机满足了专用宽幅大型板片模压成形的要求。
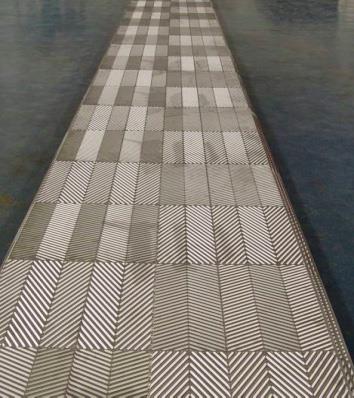
图6大型板壳式换热器专用板片
(2)开发了氩弧焊/电阻焊焊接工艺,配套专用自动程控焊机,实现了板束结构的参数化程序化焊接。两板片边缘直接焊接,焊接输入能量小,自动化程度高,焊接效率高。
(3)在设备整体结构方面,开发了适合于大型板壳式换热器的新型进料喷雾分布器,分布效果好,保证了进料液与循环氢的充分混合。研制出超大型板壳式换热器的可拆结构。轴向设置高低温膨胀节解决了设备中心线方向的热膨胀问题,热补偿性能良好。板束与壳体之间采用新型柔性连接结构克服板束在高温工作时由于热膨胀产生的径向力,有效地防止设备高温热膨胀造成的损坏。
(4)大型板壳式换热器已在福建联合石油化工有限公司140万t/年连续重整装置(9500m2 进料换热器)和中国石油乌鲁木齐石化公司100万t/年芳烃联合装置330万t/年异构化装置异构化装置(10500m2 进料换热器,如图7所示)上成功投用。
(5)国产大型板壳式换热器的综合性能已经达到国外先进水平,国内外性能对比如表4所示。
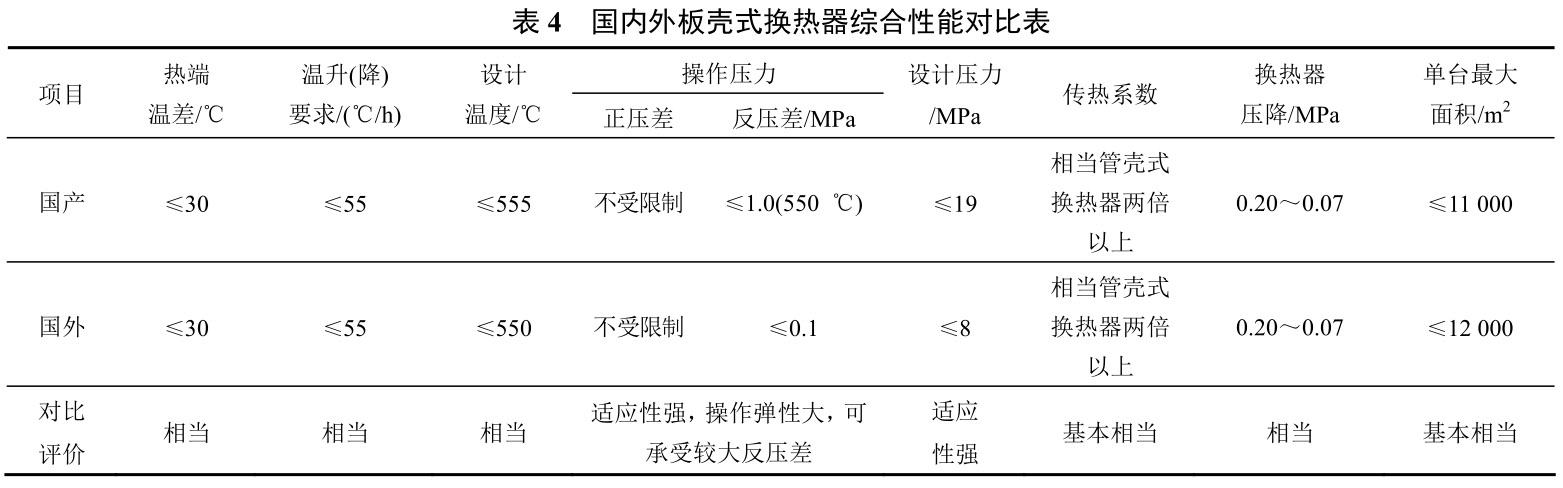
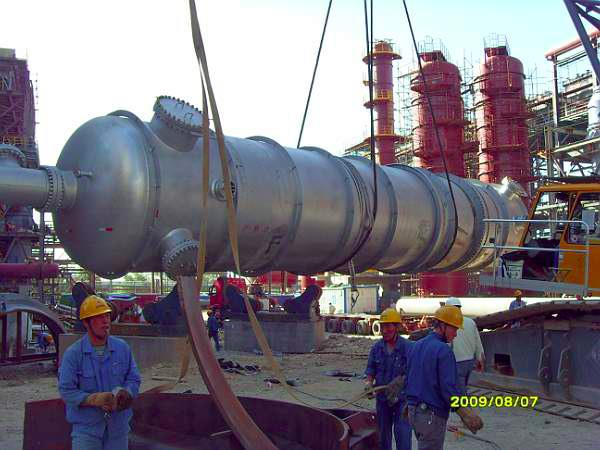
图7正在吊装的乌石化异构化装置异构化进料换热器(10500m2 )
4、存在的问题
大型换热器的国产化标志着我国过程能源装备的一个进步,但是设备背后还有更深层次的技术问题有待研究探索。
4.1大型换热器传热与流动的工艺设计
由于我国许多成套装置工艺(尤其是化工工艺)的软件包是从国外购买的,在换热设备的选择上国内并没有多少发言权。大型换热器在传热与流动上的机理有其明显的特殊性,最典型就是混合介质的局部冷凝和整体冷凝[9]。在大型换热器内实际混合物的冷凝过程介于整体冷凝和局部冷凝之间。流体入口段,工艺条件保证了较高的流速,剪切力起主导作用,截面的气液两相混合较好,近似整体冷凝。而出口处的工艺条件会造成两相分层,重力起明显作用,接近局部冷凝。冷凝器设计软件主要基于冷凝侧当地传热膜系数的准则方程,并对气相扩散阻力进行简单修正。由于气液两相界面附近的气相浓度梯度,扩散阻力降低了有效传热膜系数。尤其在低热通量条件下,当地传热膜系数的准则方程的不确定度很高。因此设计软件不能反映混合物冷凝的实际传热过程。
另外设计过程一般不考虑壳程冷凝流体的不均匀性。对于混合物冷凝,诸如回流、涡旋、旁路及流动死区等现象造成实际流场与理想流场的偏离。非理想流场的影响可显著降低混合物冷凝器的性能。
超临界混合组分流体在换热器的传热与流动的研究往往受到试验手段的限制,在设计中借用了纯物质的准则方程,因此其传热与流动的设计和实际工况还有一定的差距。
4.2大型换热器对高效传热元件的采用
对大型换热器来说,其安全性往往是放在第一位的,许多大型管壳式换热器采用的是光滑传热管,这也说明大型管壳式换热器有更大的节能提升空间。
表5和表6对比了应用三种换热管分别给大型管壳式换热器(低压混合制冷剂/丙烷蒸发器和丙烷冷凝器)带来的设备尺寸和重量的变化[10]。
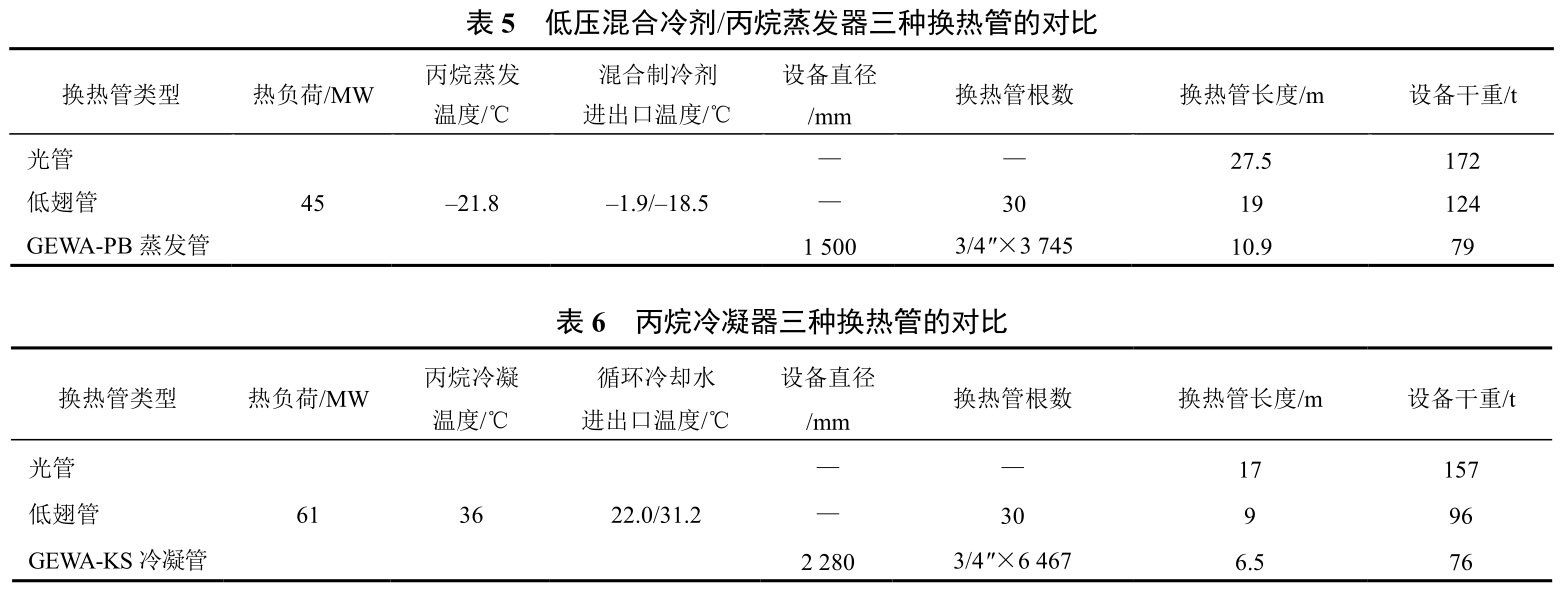
我国的高效换热管不仅在大型化的应用上较少,材料的种类也不够丰富。目前的高效换热管主要以碳钢、不锈钢、铜及铜合金为基材加工或烧结而成,在许多特种材料高效换热管的研究上还是空白。
4.3LNG领域大型缠绕管式换热器的攻关
LNG的利用在一个相当长的时间内将是我国能源战略的一个重要内容。在液化过程中的主低温换热设备的研制是重要的技术保障。我国目前的液化能力很小,采用的多为板翅式换热器。西方国家在大型LNG装置中大都采用缠绕管式换热器[11]。
不同工艺流程设置了不同的缠绕管式换热器的组合,但归结起来的技术难点如下:混合冷剂和天然气之间(超临界混合介质)的传热与流动、大型换热器特有的流体分布技术、大型缠绕管式换热器的结构研究、超长铝合金换热管及其他材料的研究。目前我国基于100×104~150×104Nm3/d天然气液化装置低温缠绕管式换热器的攻关正在讨论中。
4.4大型换热器的可靠性研究
大型换热器的可靠性涉及到许多交叉学科的问题和制造技术问题。从全世界的范围来看,换热器的失效破坏主要有4个方面:①换热管与管板的连接接头的制造质量;②腐蚀环境与传热元件材料的适应性;③换热器的振动破坏;④热应力引起的破坏。
对大型换热器来说,换热管的数量大,换热管的壁较薄,换热管与管板的连接接头质量对大型换热器的可靠性影响概率显著增大。另外由于大型换热器的换热管较长,换热器的支撑设计尤为重要,流固耦合等许多技术问题需要考虑。由于无支承跨距设计不合理造成的破坏时有发生(图8),它不仅会造成折流板和换热管之间的损伤,也会造成换热管与管板的连接接头的损伤。另外,大型换热器管束或板束的长度大,也提高了热应力破坏的可能性。
更为严重的是,上述几个因素的交互影响,降低了大型换热器的可靠性(图9显示了由于多种因素造成的板壳式换热器的破坏)。因此,要充分认识大型换热器的诸多难题,在设计和制造中制定严格的技术对策和控制措施。
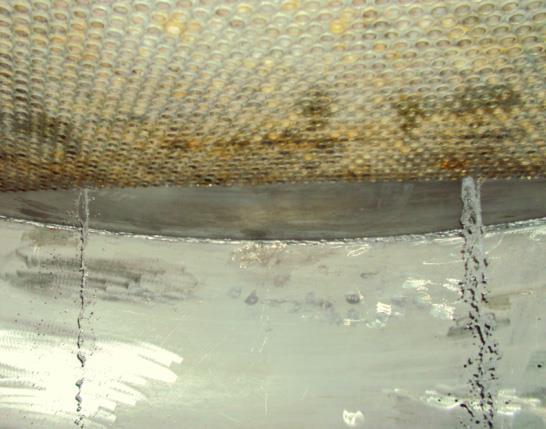
图8某大乙烯装置中由于振动破坏引起的泄漏情况
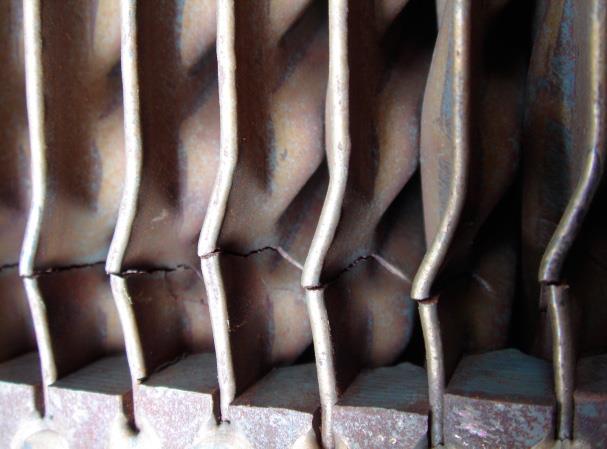
图9某炼油装置板壳式换热器的失效情况
5、结论
我国大型换热器的技术在“十一五”期间取得了显著的进展,解决了重点国产化产品的一系列关键技术,研制产品已经投入了工程应用。
(1)大型管壳式换热器在材料研究、结构设计、管板制造、管束支撑、组装检测等技术都取得了突破,能够实现长度30m以内的高精度奥氏体不锈钢无缝换热管的国产化,具备了制造10000m2 以上大型管壳式换热器的技术和能力。
(2)我国在煤化工领域缠绕管式换热器的成套技术已经达到国际先进水平,具备制造7000m2 以上大型缠绕管式换热器的技术和能力,并创新了大流量下低温甲醇洗系统原料气冷却的工艺流程。在世界上首先推出新型加氢裂化工艺流程,并研制成功了高压加氢裂化缠绕管式换热器。
(3)在大型板壳式换热器的整体结构设计、板片研究、成型设备、板束焊接、热膨胀吸收等关键技术上都有了新的进展,具备了10000m2 以上大型板壳式换热器的技术和能力。
在换热器的大型化过程中还存在一些不足之处,应该着手以下几个方面的工作。
(1)进一步研究大型换热器传热与流动工艺中的特殊性。
(2)大型管壳式换热器和高效传热元件的结合还有很大的提升空间,实现大型化的结构、特种材料、高效换热元件和管束支撑结构的和谐统一,将大大推进管壳式换热器的技术进展。
(3)开发与大型天然气液化装置相适应的大型缠绕管式换热器。
(4)提高大型换热器的可靠性,引入基于可靠性和寿命的设计和制造理念。在大型管壳式换热器的防振设计、管板设计、换热管与管板连接技术和检测技术、大型板壳式换热器的设计技术和操作控制等方面进行不断的完善。
(5)针对我国冶金工业配套技术的局限性,开发出特种合金材料换热管、超长铝合金换热管等传热元件,促进大型换热器基础技术的进步。
参考文献
[1] 张贤安. 高效缠绕管式换热器的节能分析与工业应用[J]. 压力容器,2008,25(5):54-57.
ZHANG Xianan. Energy-saving & industrial example of the high-effected wound-tube heat exchanger[J]. Pressure Vessel Technology, 2008, 25(5):54-57.
[2] 余良俭,张延丰,周建新. 国产超大型板壳式换热器在石化装置中的应用[J]. 石油化工设备,2010,39(5):69-72.
YU Liangjian, ZHANG Yanfeng, ZHOU Jianxin.Application of domestic super large scale plate shell heat exchanger in petrochemical units[J]. Petro Chemical
Equipment, 2010, 39(5):69-72.
[3] 李力,董方亮,赵石军,等. 国产首台超大型管壳式换热器的研制[J]. 一重技术,2008(6):16-19.
LI Li, DONG Fangliang, ZHAO Shijun, et al. Research and manufacture of the first domestic super size shell and tube heat exchanger[J]. CFHI Technology, 2008(6):
16-19.
[4] 李鱼,张颖. 大型管壳式换热器设计制造技术[J]. 一重技术,2011(6):25-27.
LI Yu, ZHANG Ying. Large shell-and-tube heatexchanger design & construction[J]. CFHI Technology,2011(6):25-27.
[5] 张中清,吴晓红,陈永东,等. 一种柔性连接环的碟形管板换热器:中国,201210036906[P]. 2012-07-11.
ZHANG Zhongqing, WU Xiaohong, CHEN Yongdong,et al. A type of disc tubesheet heat exchanger with the flexible elink ring:China, 201210036906[P]. 2012-07-11.
[6] 李永泰,郭春光,张中清. 丁醛转化器应力分析计算[J].压力容器,2011,28(11):29-35.
LI Yongtai, GUO Chunguang, ZHANG Zhongqing. The finite element stress analysis of butyraldehyde converter[J]. Pressure Vessel Technology, 2011,28(11):29-35.
[7] 何文丰. 缠绕管式换热器在加氢裂化装置的首次的应用[J]. 石油化工设备技术,2008,29(3):14-17.
HE Wenfeng. First application of spiral wound heatexchanger in hydro-cracking unit[J]. Petro-Chemical Equipment Technology, 2008,29(3):14-17.
[8] 余建良. 低温甲醇洗缠绕管式换热器的优化设计及应用[J]. 化肥设计,2011,49(2):23-25.
YU Jianliang. Optimal design and its application for spiral tube heat exchanger of low temperature methanol wash plant[J]. Chemical Fertilizer Design, 2011,49(2):23-25.
[9] 陈永东,周兵,程沛. LNG 工厂换热技术的研究进展[J].天然气工业,2012,32(10):80-85.
CHEN Yongdong, ZHOU Bing, CHENG Pei. Research progress in heat transfer technology in LNG plants[J]. Natural Gas Industry, 2012,32(10):80-85.
[10] THOMAS L,BRIGITTE P. Dual enhanced tubes for thehydrocarbon processing industry-from debottlenecking to grassroots[C]//LNG-16 Conference, London:InternationalTrade and Events(ITE) Group Plc,2010:1-11.
[11] 陈永东,陈学东. LNG 成套装置换热器关键技术分析[J]. 天然气工业,2010,30(1):96-100.
CHEN Yongdong, CHEN Xuedong. Analysis of key technology for heat exchanger in LNG complete set of equipment[J]. Natural Gas Industry, 2010,30(1):96-100.
作者简介:陈永东(通信作者),男,1968 年出生,教授级高工,合肥通用机械研究院压力容器与储运装备工程部部长,压力容器学会换热器委员会常务副主任委员,全国锅炉压力容器标准化技术委员会热交换器分委会委员。主要研究方向为石油、化工、天然气等领域换热设备的传热工艺研究与结构设计开发。
E-mail:chenyongdong@hgmri.com
相关链接