换热器是磷化工生产过程中常用的压力容器设备,按其作用原理分为混合式换热器、蓄热式换热器、间壁式换热器。在化工生产中用量最大的是间壁式换热器,其主要结构形式可分为列管式换热器、夹套式换热器、蛇管式换热器、套管式换热器、板片式换热器等。列管式换热器因其结构坚固、适应性大、制造工艺成熟等优点成为磷化工生产过程中的主要换热设备,但由于管板与换热管的焊接接头较多,并且受壳程与管程存在压差和温差、介质腐蚀和介质流动磨蚀等因素的影响,管板与换热管焊接处极易泄漏,导致换热器壳程与管程内介质混合,换热器达不到运行效果。如何更好地保证列管式换热器的制作质量,避免或减少因换热管的泄漏而造成系统停车的损失,笔者结合换热器制作的相关标准要
求,对列管式换热器的组装、焊接等关键工序的制作质量控制进行阐述。
1、换热管、管板、折流板的检验
1)换热管的质量直接影响换热器的使用效果,所以要从源头做好对换热管的质量控制,要选用生产能力强、质量控制严、检测手段全的企业作为换热管的合格供方。换热管采购时最好选用定尺管,要求供货方提供涡流探伤、打压等检验的相关资料;对于不锈钢、铜、镍、钛、锆等特殊材料制作的和用于双管板换热器以及盛装极度危害介质换热器的换热管,在组装之前应进行逐根耐压复验,以确保换热管没有裂纹缺陷。对特殊材料换热管还要进行光谱复验,以确保化学成分合格。另外,还要做好管径、壁厚、长度等方面的检查。
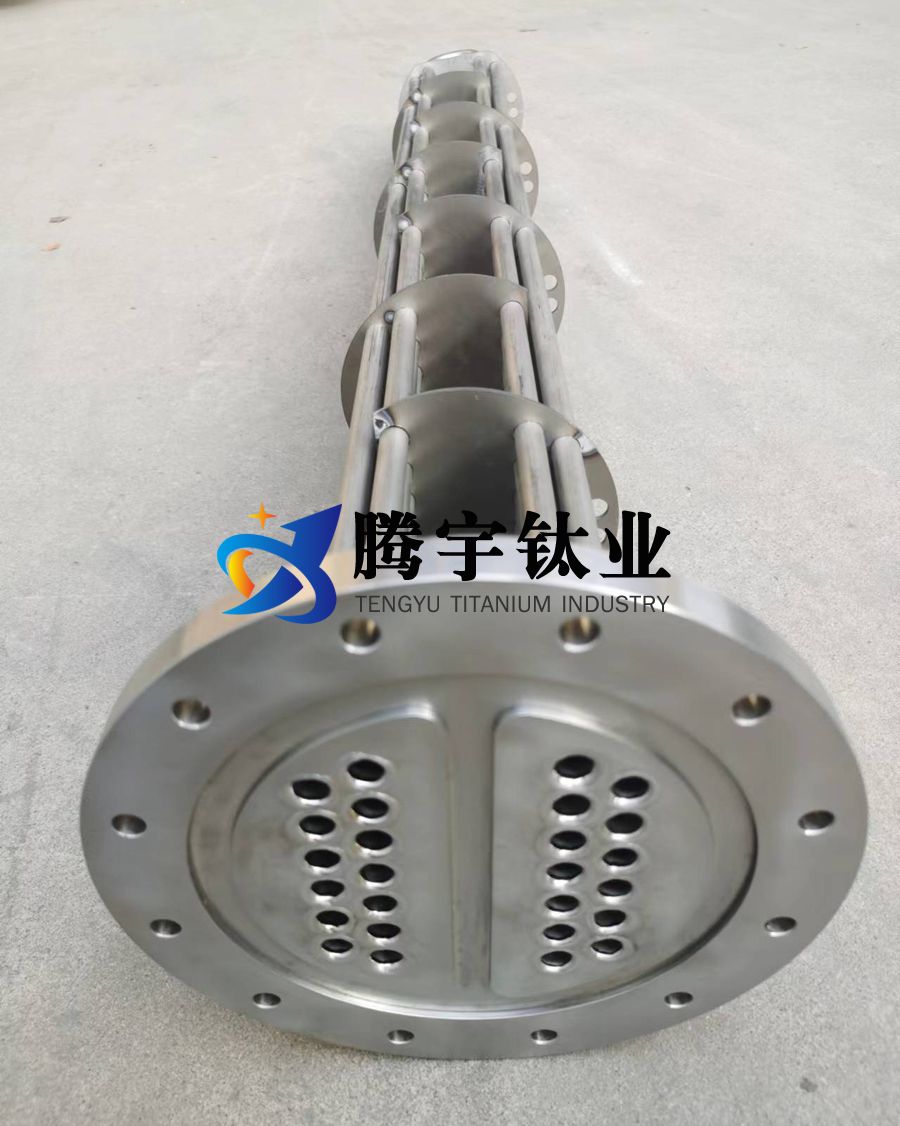
2)管板一般经煅压而成,对其内部结构要进行超声检测,确保达到设计要求的合格等级,不得有夹层、裂纹等缺陷。钻孔最好选用数控钻床,以使管孔的排布、管孔的垂直度更加精准;折流板钻孔前要进行焊接固定,每孔最好一次钻透完成,如果分次钻孔,标志一定准确、牢固;管板、折流板钻孔完成后要对管孔进行倒角,倒角角度要符合设计要求,否则会直接影响换热管的焊接质量。
2、换热管、管板、折流板的清理、组装
换热器组装前要对换热管、管板、折流板等部件的浮锈进行彻底清理,碳钢管要对管头15mm以内用磨光机打磨出金属本色。对于不锈钢、镍、钛等特殊材料的换热器要在清洁厂房内进行组装(不具备条件的要与碳钢设备制作彻底隔离),组装过程中严禁强力组装,要用木锤、皮锤等敲击需校正的部件。组装完成后,换热管要保证平齐,达不到要求的要采用合金刀具进行平头,并根据不同的焊接形式预留换出热管伸出管板的长度(熔头焊一般为1~1.5mm,角焊缝一般为3~4mm);对换热管的点焊固定要根据管壁厚度选用合适的电流,避免因电流过大造成换热管烧穿的现象。
3、换热管的胀接
对于壳程内介质腐蚀性较强或与运转设备相连接的换热器,管板与换热管的连接一般选用胀接+焊接的形式,制作中是先胀后焊还是先焊后胀,在标准上没有明确规定,根据经验,笔者倾向于先胀后焊,特别是对于管板厚度相对较薄和需强度胀的换热器一定是先胀后焊,这样可以避免由于先焊后胀对于焊缝造成的拉力损伤。根据换热管的不同材质和胀接的不同形式,胀接前要进行工艺评定,选择合适的胀接工艺参数,避免胀接不到位或因胀力过大造成换热管损伤,强度胀后必须进行气密试验,合格后方可进行焊接。
4、换热管的焊接
换热管的焊接主要分为熔头焊接、角焊缝焊接两种形式,不同焊接形式在设计上都有要求,对于压力较高特别是工作压力在10MPa以上的换热器一般不采用熔头焊接的方式。焊接前对换热管与管板要用酒精或丙酮再次进行清理,焊接处不得有浮锈、油污等杂物;为提高焊接的强度,不管是哪种焊接方式都要进行两遍焊接(管壁小于1.5mm的除外)。熔头焊第一遍可采用不加丝的自熔方式,第二遍采用加丝焊接;角焊方式必须两遍都要加丝,以避免烧穿管壁。第一遍焊接完成后,打压0.10.2MPa进行气密试验,检查焊缝处有无漏点,补焊完成无泄漏后再进行第二遍焊接,焊接完成后确保焊缝光滑、饱满;焊接过程中,最好采用“米”字形式进行焊接,避免集中连片焊接造成管板的变形。全部焊接完成后,再次进行气密试验(压力同上),无泄漏后再按设计要求进行水压、泄漏等其他试验。
5、结束语
换热器的制作是一个精细的过程,需要长期的经验积累并不断完善和改进,制作前必须弄清换热器的工作原理和不同材料的特性,根据设计要求制定合理的制作工艺,制作过程中抓住关键点并严格进行控制,确保各项工作开展规范到位,换热器的制作质量才能有充分的保证。
相关链接